15. 9. 2022
An improperly chosen magnetic separator
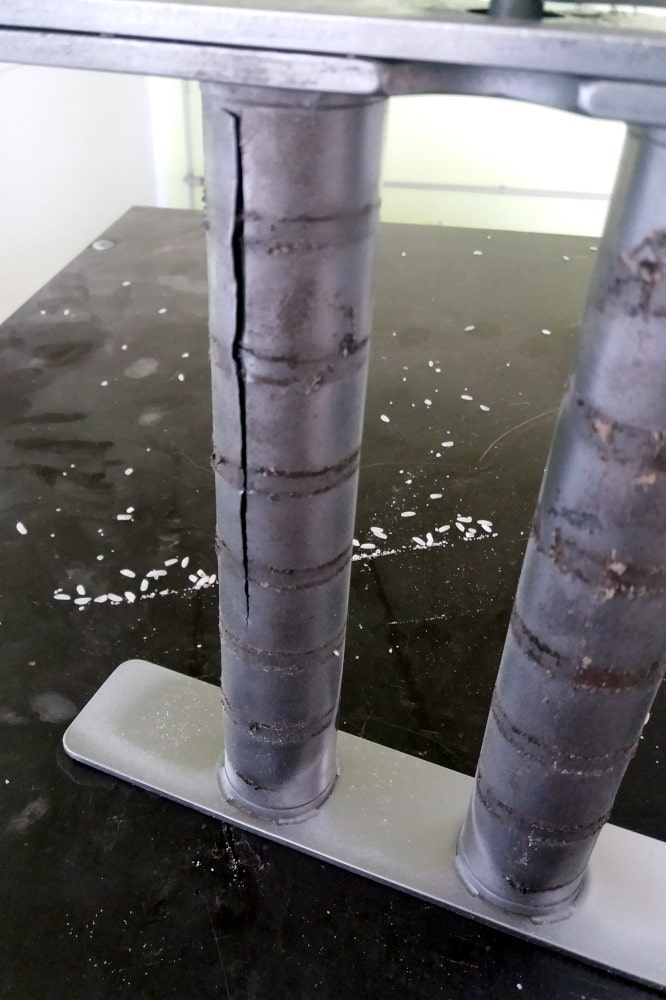
Initial status
Our client needed to remove very fine iron particles from free-flowing materials without bridging characteristics
Problem
The client bought a magnetic grate from a foreign e-shop and subsequently used the grate magnet for separation of ferrous contamination from highly abrasive material (the percentage of iron particles was very low - rather, it was a random occurrence). Unfortunately, the wall of the stainless steel protective tubes of grate separators is very thin (to achieve the highest possible magnetic induction on the surface of the protective tubes for capturing ferrous particles in micron sizes). Therefore, these separators are exclusively designed for cleaning non-abrasive materials. Due to the incorrect application of the magnetic separator, the stainless steel protective tube was damaged by the abrasive material. And as the magnetic core of the magnetic grid purchased by the client was protected only by one stainless steel tube, as soon as the surface of the protective tube was worn off, there was a real risk of damage to the magnetic core itself and the penetration of its fragments into the processed material.
Solution
The vast majority of our grate separators are equipped with a "tube-in-tube" system. This means that the magnetic cores are not protected by just one, but by two stainless steel tubes. I. e., even if the outer stainless steel tube is worn off, the magnetic core itself (encased in another stainless steel tube) cannot be damaged, and the fragments of the magnetic core cannot contaminate the cleaned material.
In any case, when selecting the proper magnetic separator, it is necessary to take into account many specific factors such as the properties of the cleaned material (size, abrasiveness, temperature, flow characteristics, type and amount of ferromagnetic contaminants), the separator processing capacity, the process issues (continuous or discontinuous production) etc. For slightly abrasive materials, we can offer for example drawer magnets like the MSR rotary separator (the material flows evenly around the entire circumference of the stainless steel protective tubes) or magnetic grates with thicker protective tubes. For a bit more abrasive materials it is possible to use also plate magnets MS-MC, hump magnets MSK or chute magnets ML, but the clients can also select drum separators with manganese steel covers (MB, MBZ) as well. And in case of highly abrasive materials, it is better to use separators that are not in a direct contact with the cleaned material (overband magnets DND-AC, suspended magnets DND-MC etc.).
Expert recommendation
Selection of the proper magnetic separator may be difficult for a layman. However, our sales and technical experts have many years of experience in the field of magnetic separation, so don't hesitate to contact them. They will elaborate a technical solution (quickly and free of charge!) that will suit your individual needs and requirements in the best possible way.