Chute magnets ML-P for vacuum and pressure pipes
Inline pneumatic plate magnet ML-P is designed to separate ferromagnetic particles especially from quickly streaming (up to 25 m/s) liquids (but also powders) of worse pouring properties. Compared with e. g. grid separators, the ML-P is suitable also for liquids containing bigger pieces of materials, fibers or abrasive particles.
Design of the inline plate magnet
The separator housing (made from stainless steel) is to be connected to a pipeline (by means of standard flanges) in order to become its integral part.
At the separator inlet there is a solid steel baffle that directs the material flow over the magnetic plates (placed at the inner parts of the separator doors) and ensures a high effectiveness of the separation process (nevertheless, the material divider is dismountable - therefore, in the case of cleaning very problematic materials, it can be easily taken out of the separator).
Ferromagnetic impurities are captured from the material flow at magnetic doors located on the separator sides. The door is equipped with very strong neodymium magnets with a magnetic induction of 7,500 G!
This separator is unique in that it can capture even very small contaminants (from 0.5 mm) even at high speeds (up to 25 m/s)!
The magnetic door is attached to the separator body on guiding rods. So sliding out it sideways and subsequent cleaning is quick, comfortable, and safe.
Which way is chute magnet cleaned?
Cleaning the plate separator is very easy:
- Loosen the screws securing the door with magnets
- Slide out the door with magnets placed on the guide rods to the outermost position
- Release the pins securing the door and turn them to the horizontal position. Secure the pins in this position again.
- Manually remove ferromagnetic contaminants trapped on the magnetic core.
Do not use metal tools to remove trapped contaminants - it could result in an injury!
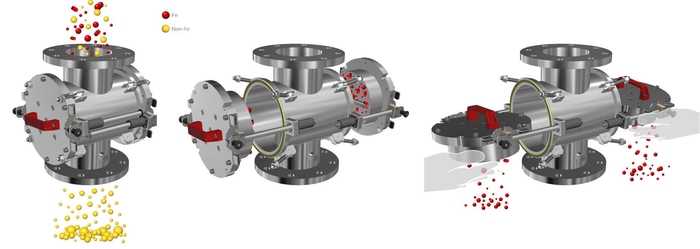
Customer care
Your project will be taken care of by us from beginning up to the very end. It does not end with the order placed at us. We will provide the full support for all the time of the use of the separator.
1. We will come
2. We will align and design
3. We will make a made-to-measure product
4. We will install
5. We will put into operation and school in
6. We will provide authorized service
We guarantee tests withing three days!
Make sure that our device perfectly meets your expectations!
We will provide tests of your material on our magnetic separators for FREE!
What pipeline is the separator connected to?
In the standard way the deep field housed magnet ML-P is produced in connecting diameters from 100 to 250 mm with pressure resistance up to 10 bar. Nevertheless, the pressure resistance, connecting dimensions and also the way of connection onto the piping system (flanges, screwed fittings etc.) can be modified according to the customer’s needs.
SOLLAU – our products are welded by real professionals!
SOLLAU certifications:
Authorization to perform welding on pressure equipment according to PED 2014 / 68 / EU
Pressure welder certificate according to EN-ISO 3834 - 2, EN 1090 - 2, EN 13480 - 1 to 5, EN 13445 - 1 to 5
- High pull strength
- Heavy-duty stainless steel design
- Pressure resistance up to 10 bar
- Excellent for abrasive and flow resistant materials
- Manual cleaning
- Vertical as well as horizontal installation
The pipe magnet ML-P is designed to separate ferromagnetic particles especially from quickly streaming (up to 25 m/s) liquids (but also powders) of worse pouring properties.
Product | Input/output diameter (mm) | Datasheet |
---|---|---|
ML-P 100 N | 100 | display PDF |
ML-P 150 N | 150 | display PDF |
ML-P 200 N | 200 | display PDF |
ML-P 250 N | 250 | display PDF |
ML-P 300 N | 300 | display PDF |
ML-P 350 N | 350 | display PDF |
Which industrial branches can the chute magnet be used in?
The pipeline magnet ML-P can be characterized by a robust stainless steel design, a big separation efficiency (thanks to the neodymium magnets), a high-capacity (no undesirable obstacles prevent the material flow in the inside of the separator body) and by an easy maintenance. The separator finds its use especially in the pulp and paper industry, because it can even deal with bridging and choking materials (like the longer fibers that are usually present in materials processed in the paper industry). On the contrary, with regard to a relatively big distance between the magnetic doors, the separator is not suitable for cleaning the materials requiring an extreme purity, e.g. in the food industry.