8. 2. 2024
Grinder protection and reduction of maintenance costs in rosin resin processing (case study)
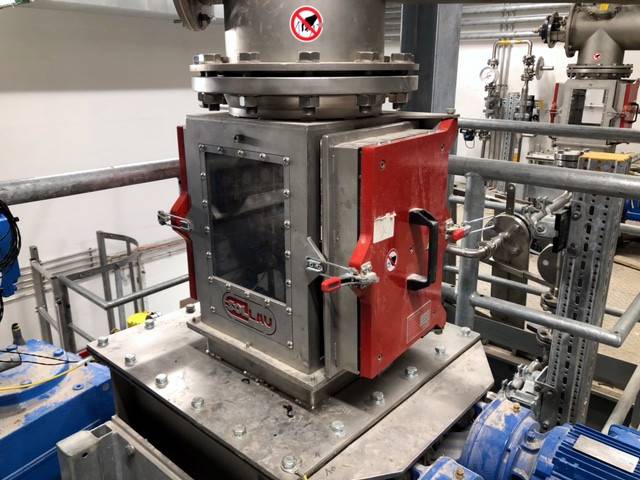
Initial status
Our customer has been engaged in the production of resins and binders for more than 100 years. His product range includes hard and soft resins, polyurethane hard resins, alkyd resins as well as various types of binders.
Problem
When processing coarsely ground rosin resin, it is necessary to ensure that the final material is free of ferrous contaminants.
That is why the protection of the resin grinder was important to the customer. Ferromagnetic particles present in the primary material can damage the grinder. The subsequent costs for grinder repairs and the corresponding production downtimes are undesirable.
Therefore, the customer requested to remove iron contaminants (especially larger ones) from the processed rosin resin to protect the grinder and reduce maintenance costs.
Solution
The coarsely ground rosin resin is transported by a screw conveyor. Between the screw conveyor and the grinder, we have installed a chute magnet equipped with the strongest neodymium magnets. Thanks to these strong magnets, we can capture not only the large iron objects (and thus protect the subsequent grinding equipment), but also fine ferrous particles. In this way, the maximum purity of the final product – the resin – is achieved.
It was necessary to use the inline chute magnet, as conventional grate separators are not suitable for this kind of material (as it would clog their magnetic grates). Therefore, we chose a separator in which the magnets are located outside the material flow (and cannot be clogged by the processed material). At the same time, however, the magnetic plates (placed at the inner parts of the separator doors) generate a strong enough magnetic field to reliably capture even very fine ferromagnetic particles.
The customer appreciated the high separation efficiency of our technical solution as well as the successful reduction of the service costs (arising especially from the production downtimes).
Benefits of using the chute magnet ML 250 N
- Grinder protection: The separator effectively traps ferrous particles, which greatly reduced the risk of damage to the crusher.
- Increased product quality: Resin without iron contamination = high-quality resin
- Reduction of grinder repair costs
Applied equipment: Chute magnet ML 250 N
Advantages of the chute magnet ML 250 N
- Separation of magnetic particles from 0,5 mm
- Ferrite and neodymium variants
- Made-to-measure separators
- Excellent for abrasive and flow resistant materials
- Magnetic strength up to 7 500 Gauss on the stainless steel protective cover
- High processing capacity (up to 150 m3/h)