25. 1. 2024
How to remove ferrous metals when recycling post-industrial and post-consumer plastics? (case study)
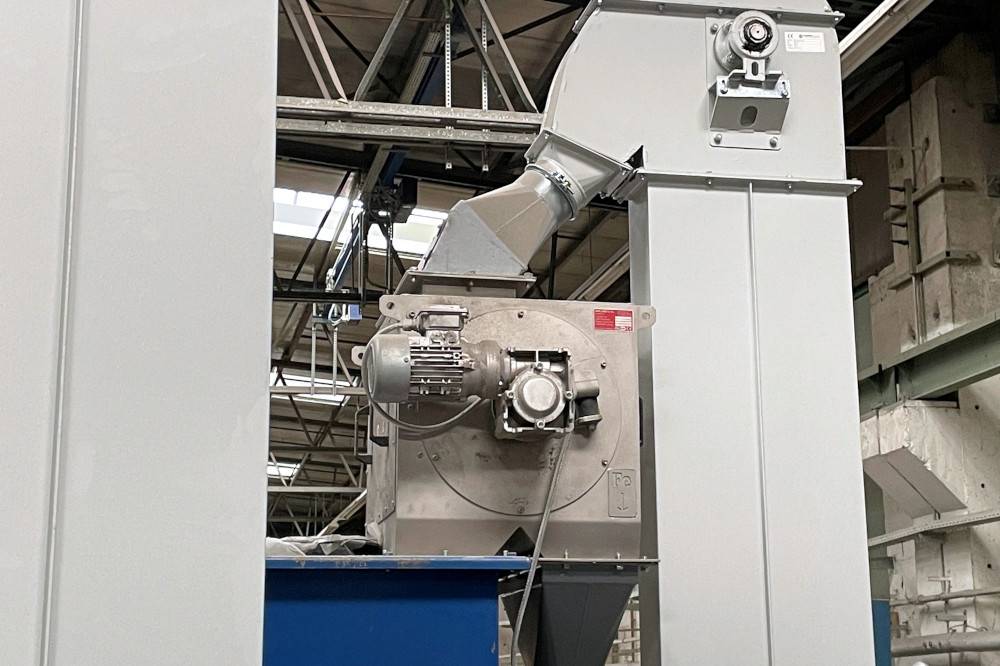
Initial status
Our customer has been specializing in recycling technical plastics and trading in secondary raw materials for more than 30 years. Thanks to our client's activities, more than 70000 tons of plastic waste are reused every year! The client processes post-industrial as well as post-consumer plastics.
Problem
When processing post-industrial and post-consumer plastics, emphasis is placed on the absolute cleanness of the final regenerated plastic = it must be free of metal particles. This is because the particles in the regranulate can damage the nozzles of the injection molding machines, resulting in unnecessary nozzle replacement costs (at the plastic molding plants).
Several devices are already installed in the production process to remove metal contaminants:
- Magnetic separators - for the removal of ferrous contaminants
- Metal detectors - for the removal of non-ferrous metals
As the processed plastics are heavily contaminated with metal objects, the magnetic separators need to be cleaned very frequently (to keep them working well) and the metal detectors reject together with large amounts of metal contaminants also a lot of good material.
Solution
After a thorough assessment of the customer's production technology from the point of view of the magnetic separation and metal detection, we proposed the following measures to be taken:
Due to the high presence of ferrous particles, we recommended installing a magnetic drum at the very beginning of the processing line. The drum was supposed to the placed behind the vertical conveyor transporting the input material to the production technology. The plastic material from the conveyor falls by gravity into the housed drum magnet. This drum is equipped with the strongest neodymium magnets and that is why we could separate a substantial part of ferrous contaminants (including even very fine ferrous dust particles) already in this first step.
Benefits of using the magnetic drum MBZ 304 N 500 GRIZZLY:
We have installed this very powerful magnetic drum in enclosed design at the point where the plastic material enters the production process. Thanks to the fact that we separated the vast majority of ferromagnetic particles, the iron contamination of the material decreased rapidly. This resulted in the fact that the magnetic separators already installed on the processing line are now used only for the final material cleaning. Therefore, it is not necessary to clean them as often as before and the possibility of human error is eliminated (sometimes the operator forgets to clean the magnetic separator, and then the separation results are of poor quality).
Since the regranulate is free of ferrous contaminants, now the metal detector detects and discards only non-ferrous metal particles. That is why the quantity of detected and separated metal particles is significantly lower, which also led to a reduction in losses of good material.
The intensification of magnetic separation (by adding another separation step = the magnetic drum) significantly improved the quality of the final material.
Applied equipment: Magnetic drum MBZ 304 N 500 GRIZZLY
Advantages of the magnetic drum MBZ 304 N 500 GRIZZLY
- Automatic cleaning without a need of interrupting the flow of material
- Adjustable material distributor to regulate the material input
- Variable attitude of the detacher of the cleaned material and separated contaminants
- Blades prevent from abidance of the fine or sticky material on the surface of the drum
- Ferrite and neodym design
- Quick and easy change of the position of the magnetic core
- Sophisticated structure with more access holes and service openings
- Up to 4 800 Gauss on the drum surface
- ATEX certificate
- Five-year waranty for the magnetic core