12. 11. 2022
Mobile equipment for metal separation from liquids (case study)
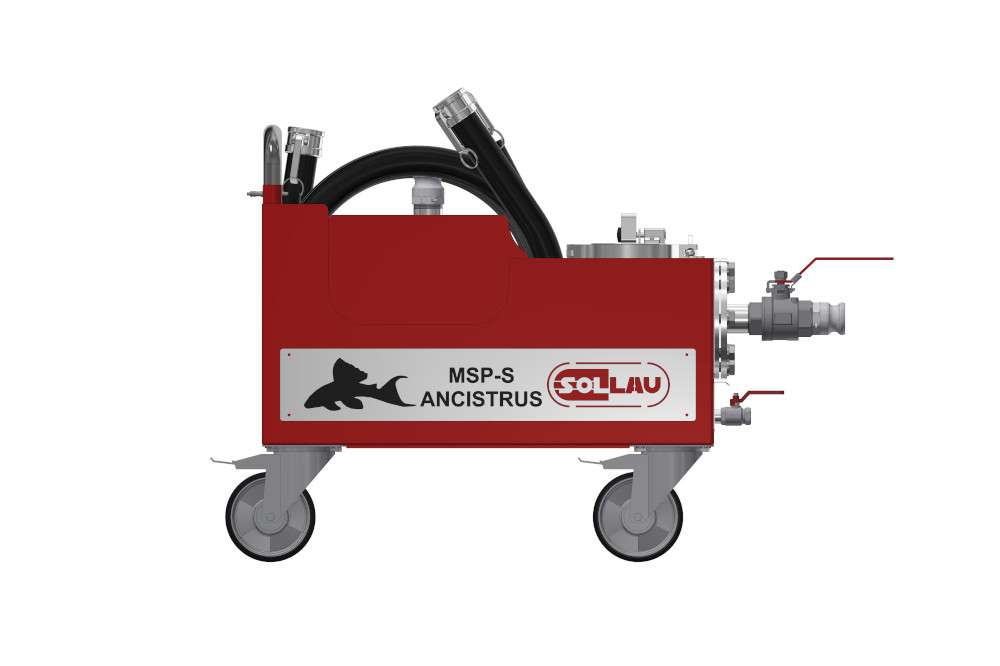
Initial status:
In many industry branches, there are very few scheduled production shutdowns. But what to do if serious problems occur in operation and the planned downtime is still a long way off? Our client (an oil refinery) got into a similar situation using hydraulically controlled slide valves to maintain the exact pressure between the reactor and the regenerator. Operations of part of the refinery, therefore, depend precisely on the reliability of these valves (loss of pressure regulation can lead to very serious problems). Therefore, the assignment that the slide valves stop reacting properly was an alarming signal for our client.
Problem description:
After checking the condition of the valves, the refinery technicians concluded that the valves get jammed due to contaminated hydraulic liquid. The carbon steel hydraulic fluid tank began to corrode. A very fine rust layer accumulated on the tank inside, and during the subsequent fluid movement in the piping system, these fine particles got (despite the installed 10-micron stationary filters) up to the slide valves. Due to the impossibility of premature shutting down the manufacturing process of the refinery to replace or clean the tank, it was necessary to find a quick (and if possible inexpensive) temporary solution how to remove weakly magnetic particles in size of fewer than 10 micrometers from the hydraulic piping system.
Problem-solving:
After consulting with SOLLAU, the client borrowed the MSP-S ANCISTRUS portable filtration system and connected it to the pipeline hydraulic system. The MSP-S ANCISTRUS thus pumped hydraulic fluid from the main supply pipe, where there was most contamination due to tank corrosion. It also captured small ferromagnetic particles and pumped the cleaned fluid back into the return pipe. After just one cleaning cycle, the content of ferromagnetic particles in the hydraulic fluid dropped several times. After a few hours of filtration, these contaminants only occurred sporadically in the hydraulic system (less than 1% compared to the original situation). This phenomenal result led the client to immediately purchase our mobile cleaning unit and use it until the planned shutdown of the production line. (The entire hydraulic circuit was chemically cleaned and flushed, including the complete modernization of the filtration system.)
Financial benefits of our solution for the client
The costs of the eventual refinery shutdown (together with the repair of the pipeline hydraulic system) would be in the six-figure sums - so the return on the purchased separator was more or less immediate.
Expert recommendation:
The MSP-S ANCISTRUS mobile filter system is an indispensable helper in many specific applications: it can be used (similarly to the case above) as an emergency tool when solving a critical situation. It is also used, e.g. by service companies that clean circuits with technical liquids, in which there is a lower occurrence of ferromagnetic particles. (Therefore it would not be worth for their operator to purchase a stationary magnetic separator.)
However, the MSP-S ANCISTRUS can also be used in some other cases:
- during pressure cleaning of oil tanks or sumps (the so-called power flush, when deposits are pushed out of the tank bottom using the ANCISTRUS pump)
- by connecting the cleaning adapter to one of the mobile separator hoses, settled iron contaminants can be sucked off from the walls of the tanks, (the so-called wand flush)
- with help of integrated hoses, the technical fluid can be pumped from one tank to another and cleaned at the same time, (the so-called transfer cart)
- compared to the downfall drain, cleaning tanks of contaminants with the ANCISTRUS pump is much faster and easier (the so-called system drain)
- the Ancistrus can be permanently connected to the pipe system and used as an external pipe system (so-called offline filtration)
- flushing the dirt out of the technical fluid tank is easier and better if the waste oil is pumped out with the ANCISTRUS pump - rather than just by gravity draining out
- with the help of a mobile filter system, e. g., new pipes or hoses can be cleaned before their installation into the pipe system (because fragments of iron objects, magnetic dust, etc. could get into them during transport and storage - this is the so-called hose cleaning).